Rotogravure Printing
Our high-speed rotogravure printing delivers precise, vibrant designs for your packaging needs. Perfect for large production runs, ensuring consistent quality and efficient turnaround times. Ideal for food and medical brands seeking reliable, cost-effective solutions.
What Is Rotogravure Printing?
Definition: Flexographic printing is a form of relief printing that employs flexible plates made from rubber or photopolymer. This method is particularly well-suited for high-volume jobs and is known for its ability to produce sharp images and vibrant colors quickly and cost-effectively.
Substrates: Flexo can print on a wide range of materials, including paper, plastic films, metallic films, cardboard, and non-woven fabrics. This versatility makes it ideal for packaging applications, labels, newspapers, and other printed materials.
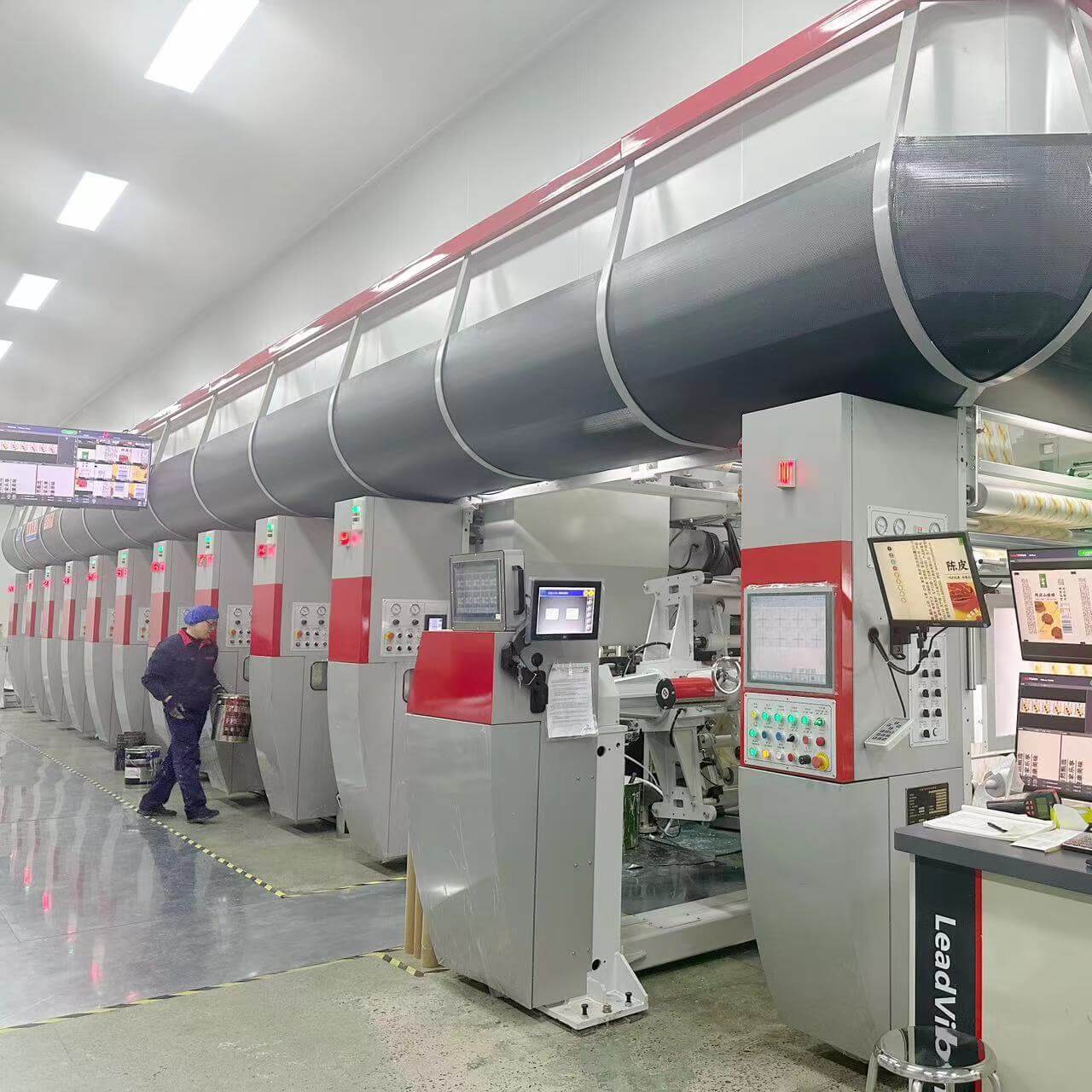
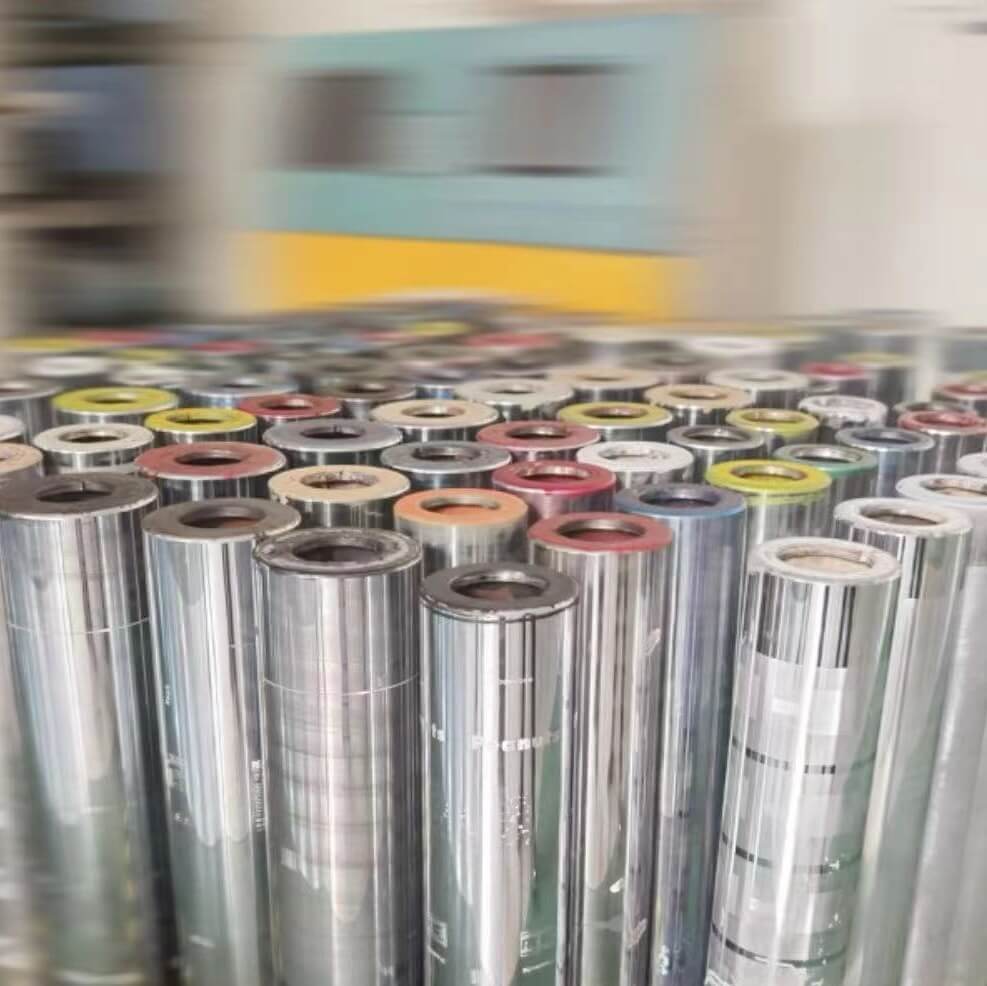
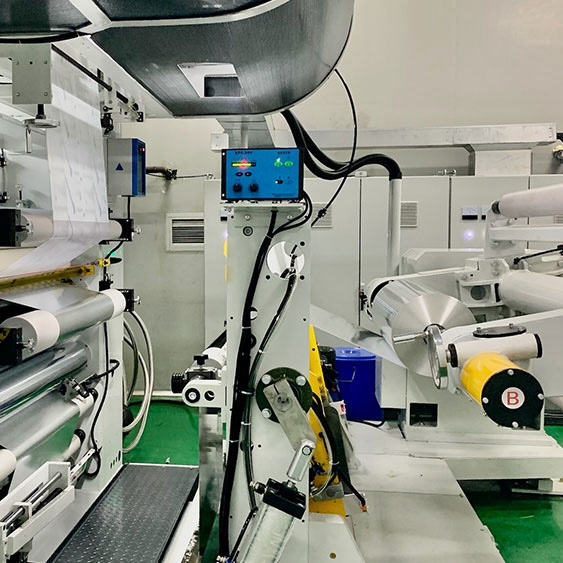
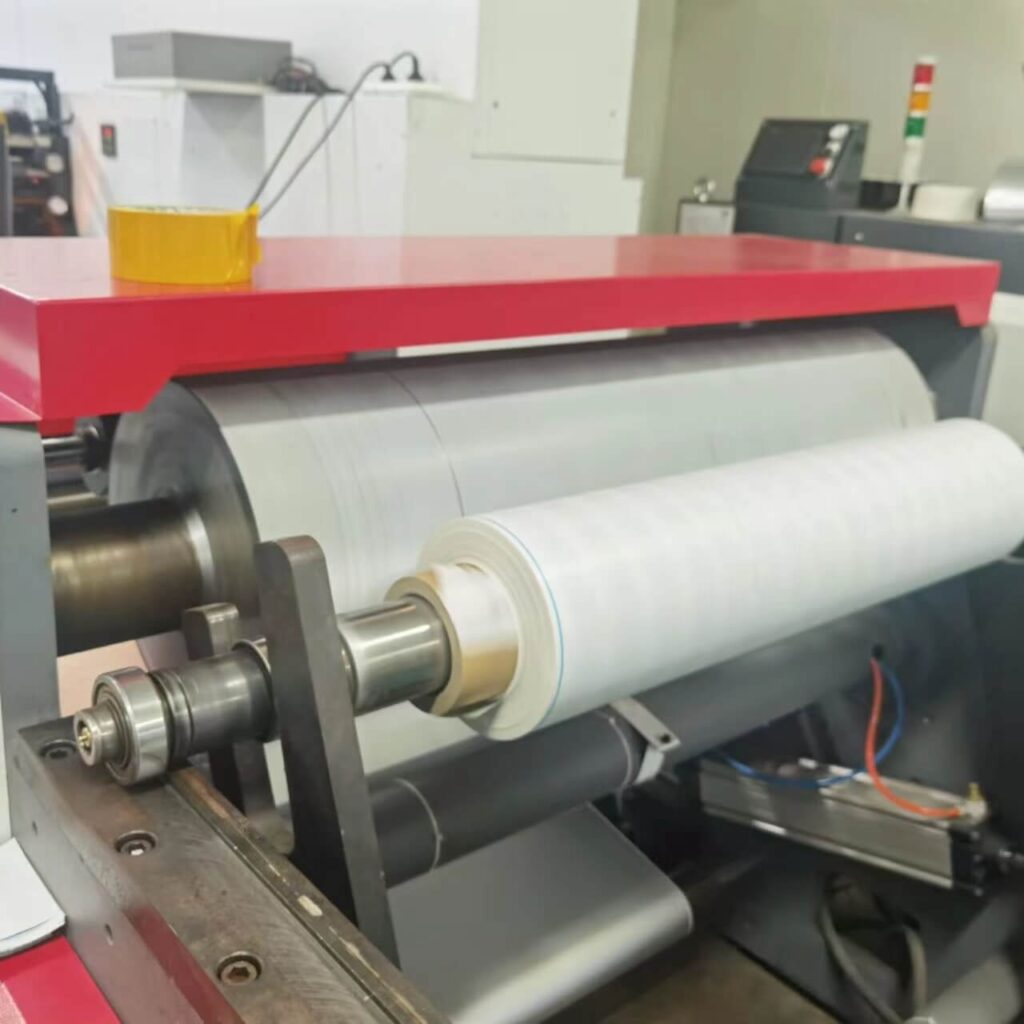
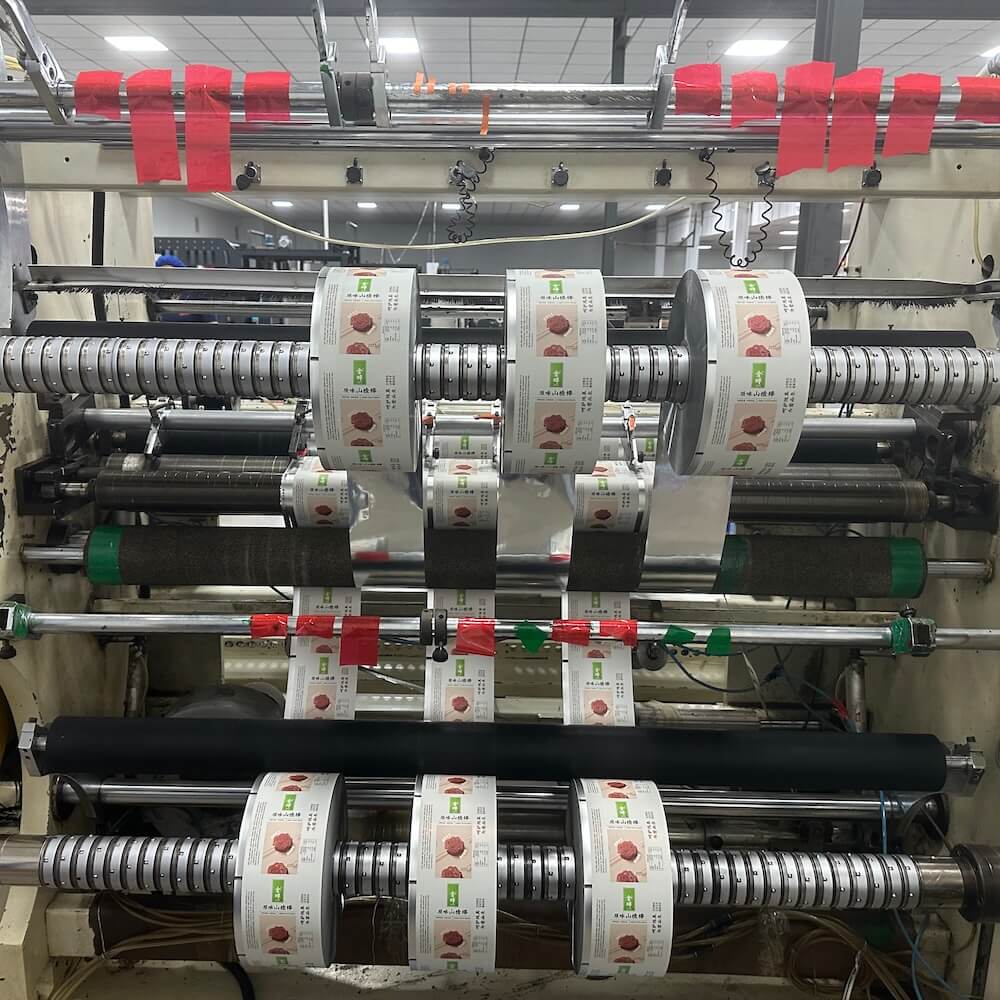
Key Features of Rotogravure Printing
Cylinder Engraving: The images are etched or engraved onto a metal cylinder (typically copper or sometimes aluminum) using a photomechanical process. The engraving can be done through chemical etching or laser engraving, creating thousands of tiny cells on the cylinder’s surface.
Ink Transfer: During the printing process, the engraved cylinder is coated with liquid ink, and excess ink is removed by a doctor blade, which ensures that only the ink in the recessed cells remains. When the substrate (such as paper or film) comes into contact with the cylinder, the ink is transferred from the cells to the substrate.
High-Speed Production: Rotogravure printing operates at high speeds, making it ideal for long runs of printed materials. It can print at speeds exceeding 3000 feet per minute.
Versatility: This printing method can be used on a wide variety of substrates, including thin films like polyethylene and polypropylene, making it suitable for packaging materials, labels, and various commercial products.
Rotogravure VS Flexographic
Printing Process
Rotogravure Printing: This is an intaglio printing process where the image is engraved onto a metal cylinder. The recessed areas hold ink, which is transferred directly to the substrate as the cylinder rotates. The depth of the engraving affects the ink’s thickness and color intensity.
Flexographic Printing: This method uses a flexible relief plate made of rubber or photopolymer. The raised areas of the plate receive ink from an anilox roller and transfer it to the substrate. This process is faster and more versatile for various materials.
Cost Considerations
Initial Costs: Rotogravure typically has higher initial costs due to the expense of creating engraved cylinders. Flexographic plates are cheaper and quicker to produce, making flexo more cost-effective for short runs.
Long-Term Costs: While gravure has higher initial costs, it becomes more economical for long print runs due to its durability and lower ink usage per print.
Speed and Efficiency
Rotogravure: Generally slower in setup due to cylinder engraving but operates at high speeds during production once set up.
Flexographic Printing: Offers faster setup times and can run at high speeds, making it suitable for shorter runs and quick-turnaround projects.
Substrate Compatibility
Rotogravure: Best suited for porous substrates such as paper and film materials; it excels in flexible packaging applications.
Flexographic Printing: More versatile in substrate compatibility, able to print on various materials including plastic films, non-woven fabrics, and metal.
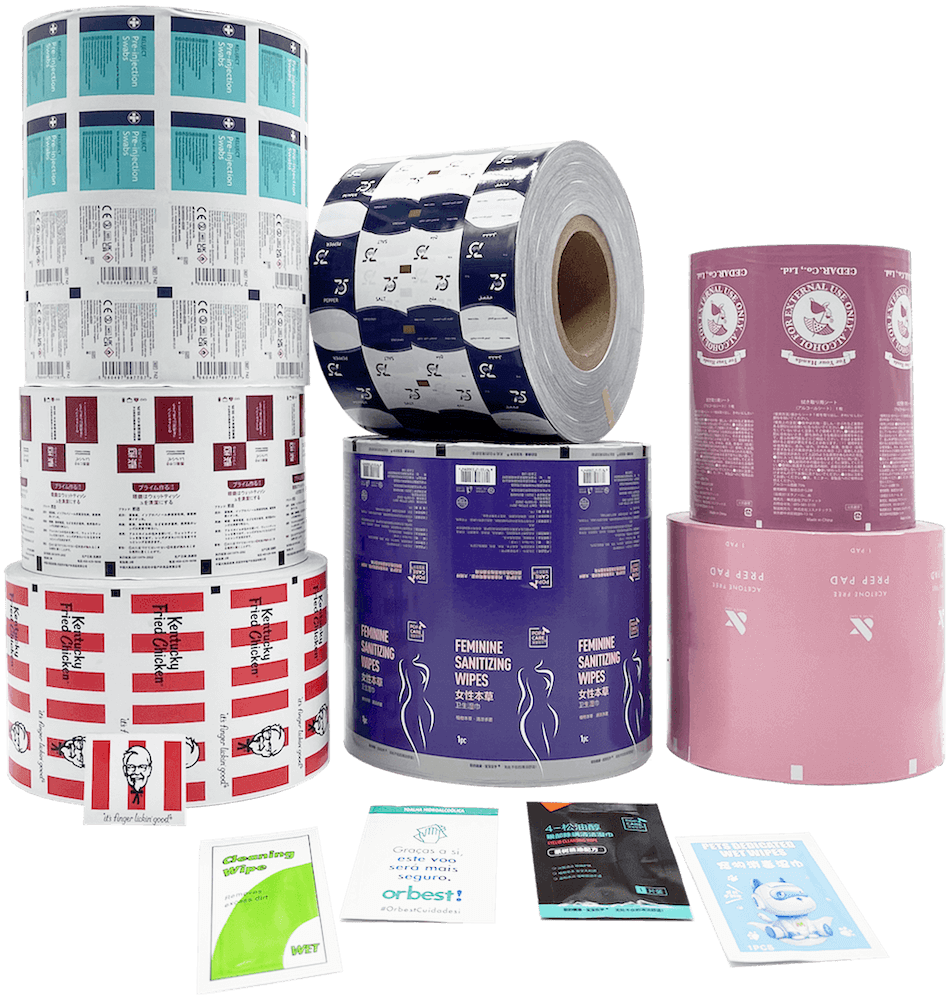
Advantages of Rotogravure Printing
Quality: Rotogravure produces high-quality prints with excellent color reproduction and sharp details.
Durability: The engraved cylinders are durable and can withstand long production runs without degrading in quality.
Cost-Effectiveness for Large Runs: While the initial setup cost is high due to cylinder creation, rotogravure becomes cost-effective for large volumes due to lower per-unit costs over time.
Contact Us to Custom Your Flexible Packaging
We’re ready to help you improve your packaging solutions here.
Common Materials Used in Composite Packaging and Properties
Aluminum Foil
Aluminum foil offers excellent barrier properties, effectively preventing moisture, oxygen, and light from penetrating, which helps maintain food quality and freshness. It is lightweight, easy to process, and recyclable, making it suitable for various food packaging applications.
Nylon (Polyamide)
Nylon possesses good mechanical strength and abrasion resistance, along with high barrier performance. It is suitable for food packaging that requires resistance to high temperatures and freezing, effectively extending the shelf life of products.
Polyester (PET)
Polyester materials have high transparency and excellent optical properties along with good barrier performance. They are commonly used in beverage bottles and other packaging, providing resistance against moisture and oxygen ingress.
Ethylene-Vinyl Alcohol Copolymer (EVOH)
BOPP (Biaxially Oriented Polypropylene)
CPP (Cast Polypropylene)
Kraft Paper
Polyethylene (PE)
Bioplastics
Production Process Videos
Stay tuned for our upcoming video series, where we delve deeper into our products and processes, showcasing how Noupack can elevate your brand.
Frequently Asked Questions
About Film Lamination
What is the difference between gloss and matte lamination?
How does film lamination enhance the durability of packaging?
How can I ensure the lamination matches my brand's colors?
What are the best practices for storing laminated products?
What is the typical lifespan of laminated packaging?
Can I request a sample of laminated packaging before placing a bulk order?
Let's Work Together
Send us a message if you have any questions or request a quote. Our experts will give you a reply within 24 hours and help you custom your flexible packaging.